Reprint from https://beautyskypackaging.com/aluminum-ingot-aluminum-tube/
Edit on Sep 27, 2022

Packaging aluminum tube is a very common packaging container in the packaging industry, it appears in our daily life frequently, just we don’t pay much attention to their existence, for example, the most common ones are toothpaste tube, hair color cream tube, glue aluminum tube, hand cream aluminum tube, ointment aluminum tube, oil paints packaging tube, some chemical industrial packing, etc…
As the amount of ointment daily products is usually relatively small, generally will be filled with smaller capacity aluminum tubes, for example, 10g aluminum tube is one of the common specifications of the ointment tube for medicine. Speaking of which, I believe that many people do not know how pure aluminum tube is produced.
It is a bit amazing to say that the raw material of an aluminum hose is actually an aluminum ingot (or aluminum sheet). This is an aluminum alloy containing 99.7% of aluminum (the remaining 0.3% is zinc, copper, magnesium, manganese, titanium, etc.).
Now with automated production equipment that is possible to take one aluminum ingot and make the final product, a packaged aluminum tube ready for filling cream products on one production line.
Aluminum ingots are produced from aluminum blocks (aluminum sheets), and in the past, we usually produced them from imported aluminum blocks from abroad, but with the maturity of domestic production technology in China, the quality is the same good quality as foreign ones, so we also started to purchase domestic aluminum ingots.
The quality of the ingot mainly depends on the composition of the aluminum content, and the 0.3% of each aluminum factory will be slightly different, in which the zinc content has an impact on the brightness of the later aluminum tube. Of course, the quality of the aluminum ingot must be good, otherwise, there will also be quality problems, for example, if there are impurities inside the ingot, then the production of aluminum tubes may be perforated that which is a serious quality problem.
How to purchase Aluminum ingots?
Aluminum ingots are not just purchased, something decided it
1. Weight: The first important is weight, but the weight of the aluminum ingot should be decided according to the tubes’ diameter, length, nozzle
2. Orifice: then that the orifices of tubes are very important too, the picture below shows that the open orifice tube must be purchased with perforated ingots and the closed orifices tube with an unperforated aluminum ingot.


3. Thread: The thread decides the weight too, if it is M15, the weight must be higher than the M11 nozzle. The long nozzle is heavier than the common thread too. That’s why the long nozzle tube has a higher price as the cost of the aluminum ingot is higher.
And why is the starting order quantity for open tubes generally higher? Because open tubes are mainly used in cosmetics and oil paints, customers purchase them more infrequently, sometimes we can’t purchase them together with other materials for other products, and we keep less stock most of the time, so we can’t produce them in smaller quantities. And the cost of aluminum material is higher too for it is a more additional process to make an open ingot. Also, in the production process, the unqualified goods are higher, so the unit price of open orifices tube is higher.
Why is the aluminum ingot rough but aluminium tube is bright?
Indeed, the aluminum sheet looks a bit rough, so why can the later aluminum collapsible tubes become bright?
This is because we have to stir-fry the aluminum sheet with special Lubricant material (lubricant sinc estereatos) before producing the collapsible aluminum tube so that the aluminum sheet is evenly coated with this material, then the aluminum sheet is smoother during the punching process, which makes the tube more beautiful and also protects the machines because rough aluminum ingots are more likely to hurt the machine.
Of course, special products, such as glue tubes, they must be lubricated with a different composition. We will not talk about this issue, for now, you can contact us if you need to know.
How does a piece of aluminum ingot become a perfect packaging aluminum tube?
The aluminum ingot is a small piece of round and flat aluminum sheet, so how are they made into a hollow, beautiful cylindrical metal tube?
- Extruding & trimming & Annealing
The first step in manufacturing a pure aluminum tube is to press the aluminum ingot into a preliminary tube shape with a stamping machine, called “extruding”. At this point, only the basic shape is formed, and the teeth and the end of the tube are still rough, so it needs to be followed by “trimming and threading” (trimming and threading) with reaming equipment, including cutting the end of the tube flush, and cutting and trimming the required threads at the mouth of the tube. At this point, the tube is actually hard and must be sent to the oven for “annealing” (annealing) to restore the flexibility of the aluminum tube. After high-temperature annealing, only then become a real “soft flexible aluminum tube”. After the aluminum tube is formed, it is not yet suitable for filling with paste (or cream, ointment) and must undergo a series of processes.
- Internal lacquer
Annealed and cooled pure aluminum tubing, followed by “internal spraying” (internal lacquering), which is a thin layer of resin sprayed on the inside of the tube wall. This resin can effectively prevent the influence of acids, alkalis, water vapor, and solvents, improve the sealing of the tube, and isolate the paste from contact with the aluminum. Also, in the case of aluminum tubes used as cosmetic packaging, health care packaging, or pharmaceutical packaging, be sure to use a resin that meets food hygiene standards for spraying. After the inner coating is done, it is cured by heating and baking.
- Priming (External lacquer)
Since most of the packaging aluminum tubes are marketed as consumer daily products after filling with pastes, it is necessary to pay attention to the appearance and have complete product information. The “base coating (priming)” is a layer of (usually white) resin applied to the surface of the aluminum tube cylinder. This resin has the property of adhering tightly to the body of the tube and is highly flexible and scratch resistant, covering the tube so that it can withstand minor scratches and impacts. After the primer is applied, it must also be baked to dry.
- Printing
The next step is to print text and graphics on the tube body. Printing is the most important part of aluminum tubes as it provides recognition and aesthetics to the product, and good printing quality can bring an intuitive sense of sophistication and show the brands to the packaging tube. Aluminum tube printing has the difference between offset printing and silk screen printing, The mainstream printing in the market is offset printing, and the more common offset printing has four-color, five-color, six-color different equipment conditions. After printing, it also needs to be heated and baked dry.
- Capping
Once the printing is completed, the “capping” (capping) can be performed. Our factory has automatic capping machines, most of the empty aluminum tubes can be capped automatically by these machines. It should pay attention to the strength of the machine when you put on the cap, otherwise, it may damage the cap. It always makes sure the threads fit the cap well.
Also, some covers (Like metal lids, fez caps, long nozzle caps) cannot be automatically capped in this procedure, so we need to skip this step and put the caps on manually when the aluminum tubes are all finished.
- End latex
The last production procedure of aluminum tube processing is “latex lining“, a circle of latex sprayed on the inside of the tube wall near the opening, referred to as the end latex. It is used to fill the gaps in the folding area when the tube is folded and sealed, in order to improve the sealing of the package.
- Packing
After the aluminum tubes are finished, workers check each tube before putting printed aluminum tubes into cartons. They won’t seal cartons after QCs re-check them again. The paper cartons must be of good quality that meet long shipping.
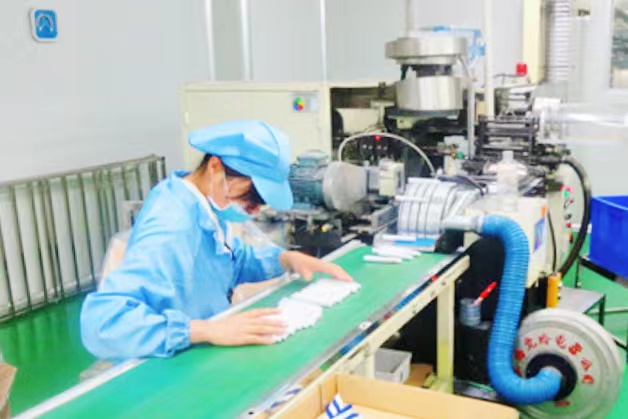
It should be noted that not all cream products request every processing procedure. For different items, In practice, the need for internal coating and end latex should be decided according to the properties of the contents, and the way of priming and printing should be decided according to the needs of product design. Although the production of aluminum packaging tubes is not a precise technology, but also pays high attention to the details of various processes, so that it can have the sealing, aesthetics, and portability of the packaging material should have, then the final filling of the completed product can have good sales, in order to play its due function in the life of consumers.