Tubes are one of the oldest and still widely used packaging for cosmetics, pharmaceutical, food, and chemical products.
Tubes are made from many metals. Square plates make to round tubes. By extrusion presses. The tubes can be made using two very different production processes now: needle-spun or deck-spun.
It’s not difficult to tell the difference between the two production techniques. Needle spinning consists of a mandrel fixed in the piston of the press giving the internal shape of the tube. By comparison, if a round tube is extruded using the bridge extrusion process, the mandrel is fixed and held by several support arms – the bridges – inside an extrusion tool.
The extrusion process is dependent on the alloy or product application. Hard alloys, for example, can only be produced by the needle spinning process.
How to make welded stainless-steel tubes?
The manufacture of stainless-steel tubes begins in the steelworks where the slabs or billets are cast. Large-diameter, thick-walled tubes are made from hot-rolled square plates, while strip-welded tubes are mostly made from cold-rolled or hot-rolled slotted pre-material. The results will differ depending on whether the stainless steel tube is hot-formed or cold-formed. Cold-formed stainless steel tubing has a smooth surface and robust mechanical properties, as well as tighter tolerances than hot-formed coil tubing.
Depending on the outside dimension, wall thickness, and end application, there are different ways to manufacture welded stainless steel tubing. Tube welded for thicker wall pipes are the main manufacturing processes for stainless steel tubes and pipes.
All welding is normally done with filler metal, except when welding under codes that do not allow the use of filler metal. After welding, the weld joint may be grounded and the pipes may be annealed and watertight as specified in the applicable standard or customer specifications. Pipes are calibrated to meet specified dimensional tolerances, followed by optional sandblasting and acid pickling. The tubes are finally tested with hydrostatic (HT), radiography (RT), or other NDT methods like dye penetrant (PT) testing, but also DT in accordance with the actual product standards.
A manufacturing method of aluminum tube cold extrusion
A manufacturing method for cold extrusion of an aluminum tubing, comprising the following steps:
1. preparing at least one tube material: the tube material is made of aluminum ingot which is more than 99.5% pure aluminum;
2. shrinking head treatment: reducing the diameter of one end of the tube material;
3. Film treatment: apply lubricant on the tube;
4. Cold extrusion treatment: prepare at least one die and at least one mandrel, so that the mandrel extends into the tube, and pushes the end of the tube that has undergone shrinkage treatment.
By driving the tube material through the eye of the eye mold, the tube material can be formed into a desired aluminum tube. The invention can not only improve and increase the strength of the aluminum tube, but also improve the processing quality and processing speed, and can effectively reduce the wastage of the aluminum material and reduce the manufacturing cost.
Aluminum alloys
Generally, aluminum alloys can be divided into two categories: heat-treated aluminum alloys and non-heat-treated aluminum alloys. These two aluminum alloys can be formed by extrusion (generally heated to 550°C), butt welding, and other manufacturing methods.
However, when the two kinds of aluminum tubes of different materials are to be artificially strengthened, they will encounter the following difficulties:
1. Because non-heat-treated aluminum alloys can only be strengthened by cold rolling and cold forging. However, this kind of strengthening treatment is only suitable for sheet or solid finished products, not for hollow aluminum tubes. Therefore, there is currently no effective method for artificial strengthening treatment for non-heat-treated aluminum alloy aluminum tubes.
2. Although the aluminum tube of heat-treated aluminum alloy can be strengthened by relevant heat treatment procedures (such as solution treatment, age hardening treatment, etc.), tube deformation and dimensional instability problems.
In addition, in order to meet the relevant size and precision requirements, the above-mentioned aluminum tubes need to be subjected to subsequent mechanical processing, such as turning, grinding, etc. Although this can make these aluminum tubes meet the relevant size requirements, however, other mechanical processing will lead to the following deficiencies:
1. Low processing accuracy, slow processing speed, and low processing stability: Since such mechanical processing uses tools and abrasives for processing, it is easy to cause processing accuracy due to processing errors.
2. High material consumption: aluminum tube materials will be lost in manufacturing and grinding, which will not only cause material waste but also increase material costs.
3. High inventory rate: Because the size changes that can be processed by turning and grinding are limited, and if the range of turning and grinding is too large, the cost of materials will be greatly increased.
4. Low design variability: It can be seen from the general turning technology that when the length of the aluminum tube is more than five times the diameter of the aluminum tube, the in-tube turning of the aluminum tube will cause technical difficulties, and when the length is more than eight times the diameter of the aluminum tube, the outside of the aluminum tube will also cause technical difficulties.
5. Low surface luminosity: After the aluminum tube is generally turned and ground, its outer surface will be covered with knife marks. Therefore, the surface luminosity of the aluminum tube will be poor.
Aluminum Collapsible Tubes
Aluminum collapsible tubes as a popular packaging material in cosmetics, pharmaceuticals are made from pure aluminum more than 99.5%.
The aluminum tubes are made from round aluminum slugs at the right diameter and weight, they are through the process of extrusion to tube, trimming to the right nozzle, length, annealing to soft tube, coating external lacquer, offset printing, assembling caps, coating internal lacquer & end latex. Then a beautiful cosmetic tube is coming.
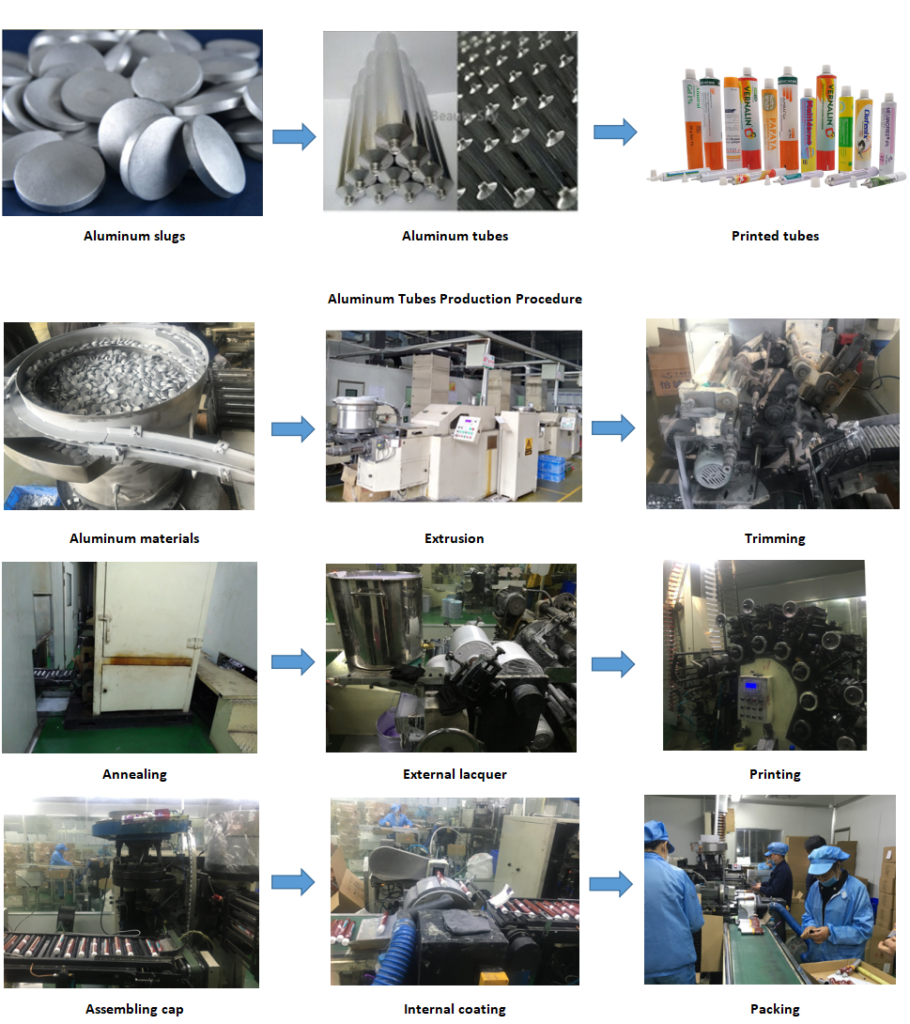
Aluminum tube 5g, cylindrical Usage: For eye ointment
Aluminum tubes come from the dust-free production plant, i.e., they are produced from a pharmaceutical point of view under strict hygienic conditions and packed in a sterile manner.
The tubes are painted neutral white or offset printing OEM on the outside and can be labeled for identification.
The 5 g tube often has a length of 80 mm and a diameter of 13.5 mm.
The screw cap is closed with an aluminum membrane, which serves as a tamper-proof seal and protects your contents until it is opened. Thanks to the piercing spike incorporated into the cap (thread M7), opening the tube cleanly is not a problem.
The tubes are filled via the open rear end, which is then pressed together using tube sealing pliers and thus sealed. The integrated latex ring ensures the necessary tightness.
The aluminum tubes are particularly suitable for filling creams, gels, ointments, toothpaste, and the like. Due to the food-safe production, the tubes are also often used in the food sector (e.g., gourmet kitchens).
If you search packaging suppliers, contact Beautysky who makes aluminum tubes for more information about the collapsible aluminum tubes, like diameter, volume, offset printing, screen printing, hot stamping, coating, orifice, sample, markets, price range, new products. Leave your message online or call us, a special offer will be provided to you. Free samples are available to be delivered to you if you give us your address.